Work Package 6 looks at the combination of LEILAC and IHCaL technologies to develop an alternative process flow. LEILAC is an indirect heating technology developed by Calix. Instead of using heat pipes to transfer the heat (as conventional IHCaL does) it relies on a long tube made of a special steel. The cement meal or limestone floats down the inside of the tube, and the combustion occurs in a furnace surrounding it. This heats the tube and then the powder, leading to calcination. The CO2 is removed from the top, and the calcined product at the bottom. This technology is already being used for manufacturing MgO that is used in many applications, including water treatment and aquaculture. A LEILAC pilot plant for limestone and cement meal is operating in Lixhe, Belgium, as part of the Horizon 2020 LEILAC-1 project. The successor H2020 LEILAC-2 project in Hannover, Germany, is looking to scale it up to separate around 20% of a European cement plant’s typical emissions at low cost, while burning typical cement fuels including coal and RDF. As well as EU funding, there are significant contributions from a range of cement multinationals.
Both end-of-pipe and integrated versions of the IHCaL cement and lime plants are possible with LEILAC technology. As around ½ to ¾ of the CO2 (i.e. the ‘process CO2’ from the limestone or cement meal) can be captured directly from the LEILAC reactor, the end-of-pipe IHCaL to capture the CO2 from the combustion can be significantly smaller if it is used in conjunction with a LEILAC system. This could save on both capital and operating costs, compared to a stand-alone IHCaL system, reducing the cost of capture. Furthermore, the simplicity and relative maturity of LEILAC technology in the cement and lime industries means that several risks associated with scaling up to full plant size are already mitigated.
Work Package 6 covers the design process from concept through to process simulation and includes a techno-economic study. As of September 2021, the process simulations are essentially complete, with focus on reaction model, control strategies and techno-economics. By the end of the project, the Consortium will have an estimate of the costs of the LEILAC-IHCaL (also known as IHCaL-DS) process to a feasibility study level.
Aside from the process simulations, WP6 has taken a qualitative deep dive into the effects on each existing process unit of applying IHCaL-DS to a cement plant. This identified several important effects about process bottlenecks and changes in process conditions. The current prospects for IHCaL-DS are positive. One benefit of the end-of-pipe configuration, apart from its relatively low energy penalty, is the ability to install CCS to a plant in stages. The LEILAC calciners can be installed first, capturing around 2/3 of the emissions in a typical cement plant for minimal cost. When more capital (or other resources, such as CO2 transport & storage capacity) is available, the IHCaL plant can be constructed. This staged approach reduces risk for plant operators and potentially brings forward the installation of carbon capture facilities by several years.
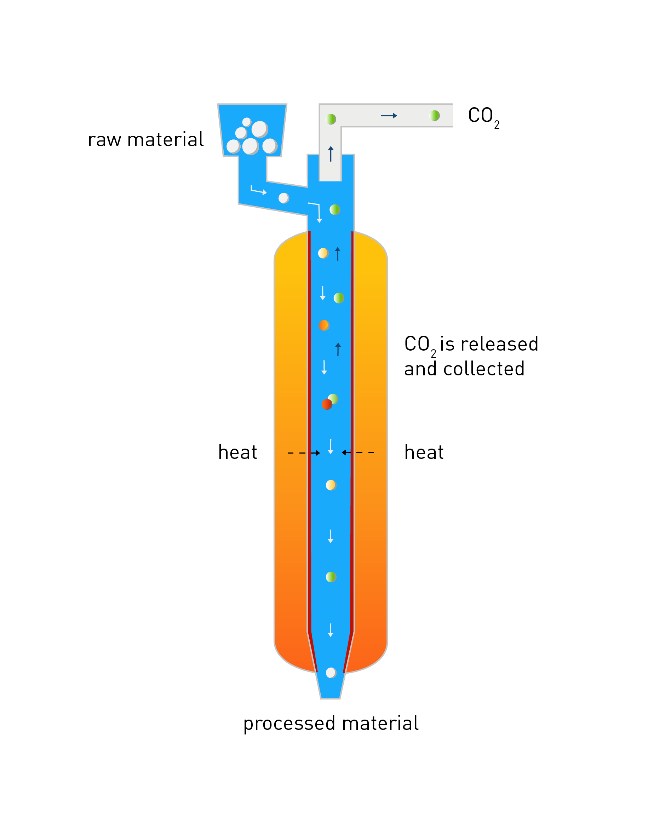
Figure 1. The LEILAC Technology
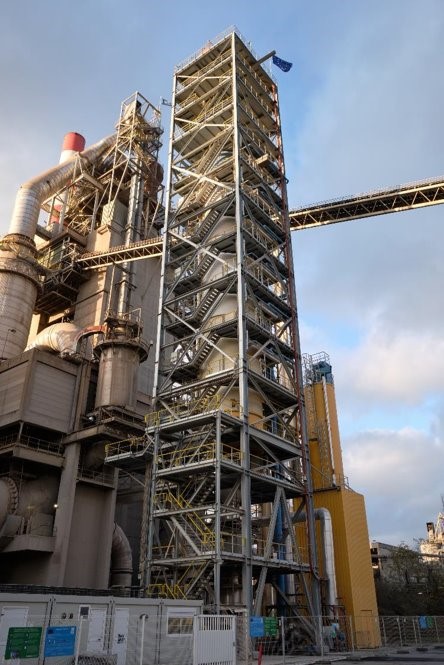