Within Work Package 1, preliminary concepts were developed for the integration of the IHCaL process into lime and clinker burning process. By implementing the process, priority was always given to high plant efficiency with maximum utilization of thermal energy.
Lime burning process (Task 1.1)
During the first part of Work Package 1, two concepts for the integration of the IHCaL process into the lime process were developed. One concept corresponds to a tail-end configuration, in which the IHCaL facility for the carbon capture is attached to an existing plant as an end-of-pipe addition. The second concept (see Figure 1) consists of a highly integrated solution, suitable for entirely new facilities. The design and integration of these plants was based on a reference lime plant of LGE in Hönnetal, Germany.
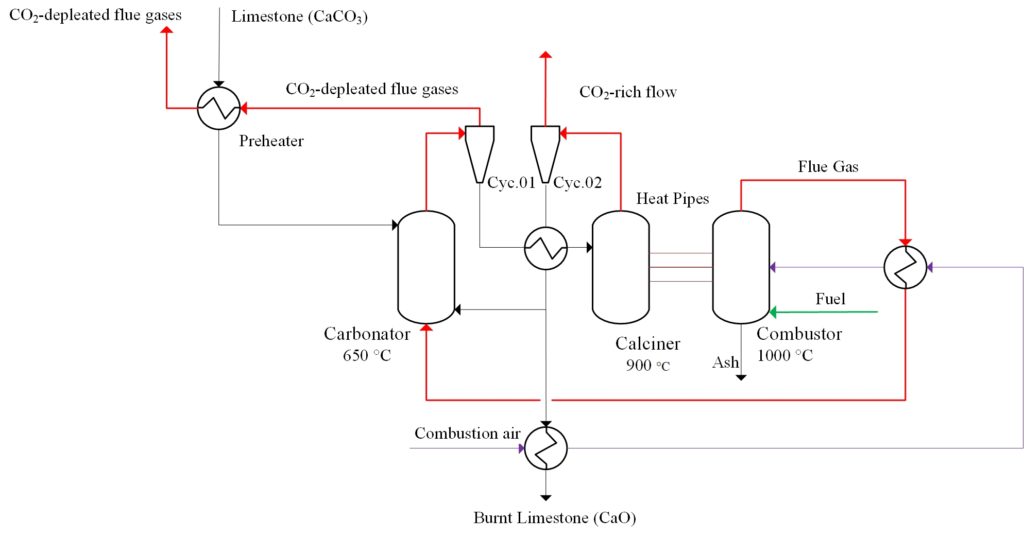
The corresponding numerical models in Aspen Plus were developed and the energy & mass balances were performed. Furthermore, a sensitivity analysis was carried out to assess the influence of the main process parameters. Critical points for integration are the preheating of the combustion air, the efficiency of the sorbent solid-solid heat exchanger, and the utilization of the sorbent purge as lime product. The first results were published in M. Greco-Coppi et al. 2021. The developed models and the obtained results will be used to further develop the integration of the IHCaL into lime plants by experimental and numerical methods.
Clinker burning process (Task 1.3)
In the second part of Work Package 1, preliminary concepts for the integration of the IHCaL process into clinker burning plants were developed. Compared to the lime burning process, the raw material mixture in the clinker burning process consists not only of pure limestone, but of other components. Portland cement clinker is produced from a raw material mixture consisting mainly of calcium oxide (CaO), silicon dioxide (SiO2), aluminium oxide (alumina (Al2O3) and iron oxide (Fe2O3). These chemical constituents are supplied by limestone, chalk and clay or their natural blend, marl. Clay minerals and feldspar are compounds of aluminium oxide and silicon dioxide (aluminosilicates) with alkalis, such as sodium and potassium. The iron oxide required for melt formation is either contained in the clay minerals in the form of ferrous hydroxide or it is added in the form of iron ore. To ensure that the cement meets the required quality standards, a precisely defined raw material composition must be maintained.
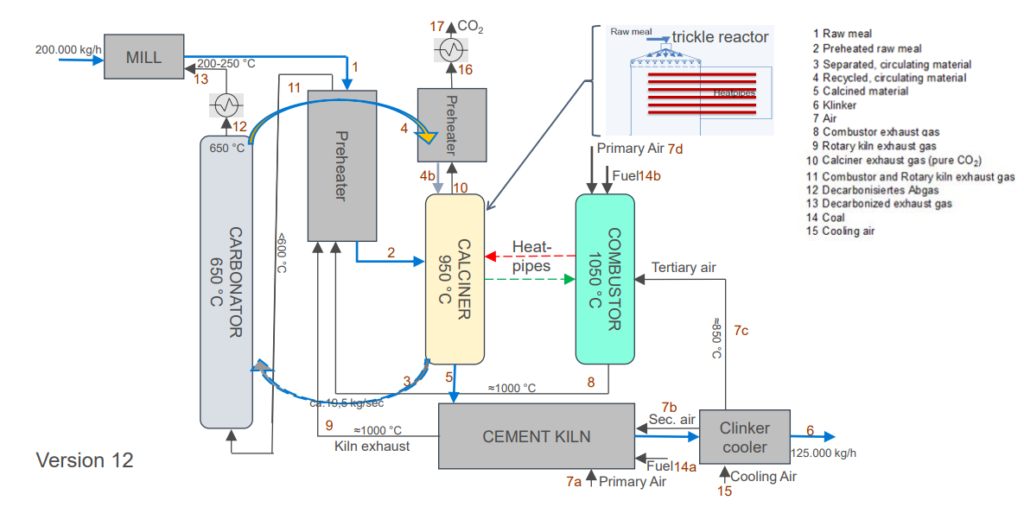
Due to the complexity of the process, the preliminary concepts have been continuously revised and enhanced on basis of experimental work and literature data, in order to find a validated process design. For this purpose, the existing VDZ process model for the clinker burning process was adapted to the new requirements. Figure 2 shows an example of the current flow diagram of the concept variant with integrated IHCaL process, which is currently being simulated in the VDZ process model on the basis of a BAT plant.
Experiments on cement raw meal (Task 1.5)
During the calcination and carbonation tests, challenges arose with regard to reactivity, agglomeration tendency and fluidization behaviour of cement raw meal, which differed from the behaviour of pure lime, observed in previous work. Therefore, additional investigations were carried out on raw meal. First agglomeration test shows that above a temperature of 820 °C the pellets begin to agglomerate, which leads to a process stop. In contrast, the fine raw meal shows no agglomeration in the required temperature range, but has problems with fluidization in terms of channel formation and material discharge. In addition, thermogravimetric investigations under CO2 atmosphere and temperatures between 630 and 980 °C revealed reduced reactivity, which can be attributed to a low free lime content and increased belite and spurrite phase formation.