Process model development
To further improve the simulation and design of the fully integrated IHCaL process, a 1D-Model of the 300kWth pilot plant reactor at TU Darmstadt is developed in Matlab and validated. It will be able to determine the heat and mass balances of the process, which will be used to upscale the process models. Two different calcination models, one from Labiano and one from Martinez, are compared, to find the one that predicts the most accurate. First simulation results suggest that, although the calciner is fluidised by air, the amount of released CO2 is so high, that no calcination takes place in the colder regions of the fluidised bed. For modelling the temperature distribution in the calciner, a one-dimensional steady conduction model is added to the heat transfer model. The validated model will be implemented into the already existing process model in ASPEN Plus. This will help to scale up the IHCaL process precisely.
CFD simulations of the calciner
One of CERTH’s major contributions into ANICA Project is to provide a validated transient CFD model of the 300 kW bubbling calciner. This model will be used to investigate the effect of several operating conditions (e.g. Geldart A vs. Geldart B particles, operating regimes) and heat pipes arrangements on the performance of the heat pipe heat exchanger. The simulations are conducted within the commercial platform of ANSYS Fluent, using numerous in-house built subroutines regarding the Kinetic Theory of Granular Flows (KTGF) closure terms, reaction kinetics, and drag force models.
The granular flow in the calciner is modelled following an Euler-Euler (TFM) approach. CERTH applies an in-house version of the sophisticated sub-grid EMMS (Energy Minimization Multi-Scale) drag model, able to accurately take into account the effect of the flow heterogeneity. The TFM model is validated against experimental data from the previous CARINA project, concerning heat transfer coefficient, CO2 production and pressure profile.
In parallel, CERTH is currently developing an Eulerian-Lagrangian model, i.e. the Dense Discrete Phase Model (DDPM), which utilizes closure terms from the KTGF. The main advantage of the DDPM methodology is that it is capable of incorporating a PSD into the model, which is a key parameter to improve the heat transfer and reaction modelling accuracy. However, DDPM has not been extensively validated especially for dense flows, compared to the TFM. As a result, its successful implementation in the complex calciner geometry is quite challenging, often requiring special numerical treatment.
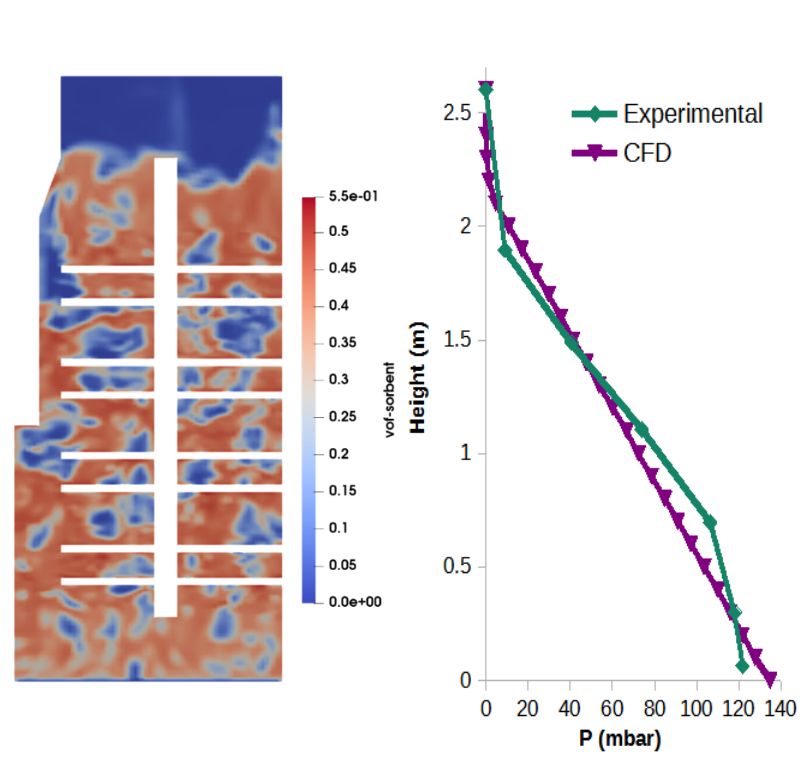
Figure 1. Euler-Euler model: volume fraction field in the calciner (left) and pressure profile validation (right).
Reactor development
In the first half of the ANICA project, the batch calciner was successfully recommissioned. A concept for a second stage calciner was developed and adapted. Before investigations regarding the second stage calciner are conducted, first tests were carried out with limestone and cement raw meal to investigate whether also cement raw meal could be a possible sorbent in a highly integrated variant of the IHCaL. Contrary to expectations, the carbonation of cement raw meal was quite complicated in the batch calciner. In summary, three challenges can be named: (1) low reaction rates of cement raw meal with CO2 in comparison to lime, (2) agglomerations that lead to defluidisation, and also (3) a difficult fluidisation behaviour due to a broad particle size distribution and stickiness of the cement raw meal and cement pellets.
All three challenges could become a reason that the highly integrated variant of the IHCaL is not applicable for cement raw meal. An objective of the ANICA project is to propose a realistic concept – tail-end or highly-integrated – for the IHCaL in a cement plant. Due to this, FAU decided to adjust its focus to investigate this open questions regarding reactivity, agglomeration and fluidisation of cement raw meal. A new task 1.5 is identified and the first results are shown in WP1.
Development of improved heatpipes
For an improved heat transfer between the calciner and combustor of the IHCaL, an optimization of the heat pipes is part of the project. In the IHCaL, horizontal heat pipes are used. The heat transfer capacity of horizontal heat pipes is limited by their capillary limit and entrainment limit. An optimization calculation was made to find the best compromise between the mesh structure for the special needs of the capillary and the vapor area. Furthermore, FAU calculated that the entrainment limit is negligible with one layer of a fine pore structure at the inside of the capillary system. Larger pores at the outside of the capillary system could make a further improvement in the backflow of the medium from the condensation to the evaporation zone. One point that should be further considered is the filling level of the working fluid in the heat pipe.
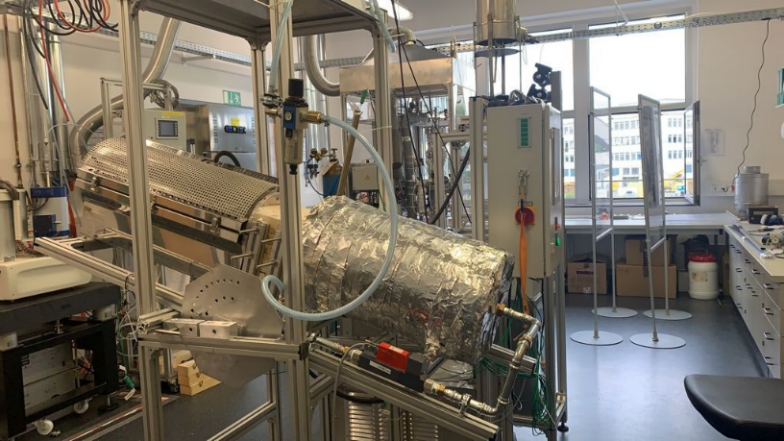
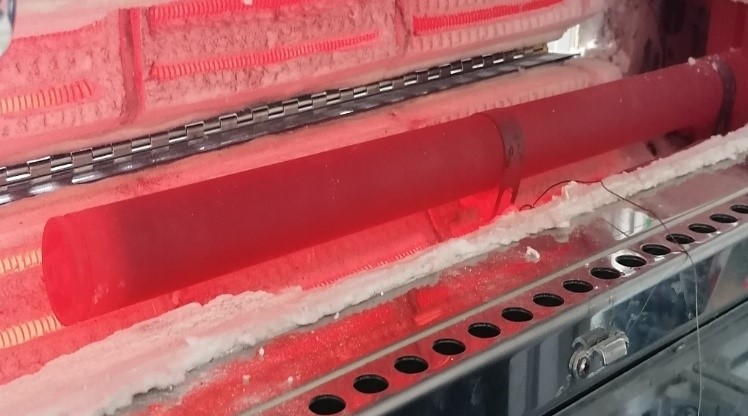
Figure 2. Picture of the test rig to measure the performance of the heat pipes (left). The test rig is rotatable to measure the capillary limits of the heatpipes. The picture (right) shows a detailed view of a heat pipe in the test rig at 800°C.