The IHCaL Process
The IHCaL process has the great advantage that raw material for lime and cement production can be used as sorbent, which significantly reduced the energy requirements (e.g. for calcination of limestone), environmental impact, and costs. Furthermore, cheap waste materials are suitable as fuel for the fluidized bed combustor, which also reduces the costs. The use of waste fuels with a high fraction of biogenic carbon opens the possibility to achieve net negative emissions. The process operates at high temperatures (> 650 °C), which allows utilization of heat for power production in a highly efficient steam cycle. Compared to standard carbonate looping (CaL), the IHCaL process avoids the need of oxygen, further decreasing the energy penalty. Hence, CO2 avoidance costs of the IHCaL process for lime and cement production plants are expected to be in a well below 25 €/t, which is close to current CO2 prices and significantly lower than competing CO2 capture solutions for lime/cement plants.
In previous work, the IHCaL process has been successfully tested with respect to CO2 capture from a of a hard coal fired power plant as a retrofit option. High CO2 capture rates for the IHCaL process of more than 90 % have been proven in previous 300 kWth pilot tests. Hence, the IHCaL process has been validated at industrially relevant conditions for power plants according to TRL 5. This project will move IHCaL technology to TRL 6 because the technology will be demonstrated at industrially relevant conditions using the same fuels, sorbents, and operating conditions as can be expected in large-scale commercial IHCaL plants for lime and cement applications. It will prepare the basis for system prototype demonstration in operational environment by the basic design of a 20 MWth demonstration plant (TRL 7). The major advancements to be expected within this project is summarized as follows.
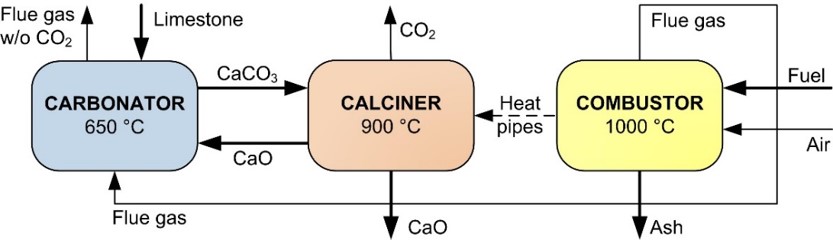
New concepts for integrating the IHCaL process with heat pipes into lime and cement plants will be developed by means of process simulations. These new concepts are expected to be superior to CaL processes with oxy-fired sorbent regeneration in terms of energy requirements since no oxygen is required. The feasibility of using spent sorbent from the IHCaL process for lime/cement production will be evaluated by dedicated tests.
Novel concepts of a solids/solids heat exchanger for heat transfer from the calciner solids flow to the carbonator solids flow and of an unheated downstream second stage calciner that uses sensible heat of the sorbent for further calcination are developed and tested in order to decrease the heat demand of the calciner. An advanced capillary structure within the heat pipes will be developed and tested for improving the heat transfer for the proposed horizontal orientation within the IHCal process.
The IHCaL process will be tested in a 300 kWth pilot plant under realistic conditions of cement/lime applications. Typical fuels of lime and cement plants (i.e. coal and SRF) will be used as fuel in combustor. A real flue gas from combustion of coal and SRF (produced in the combustor) will be fed to the carbonator. Additional CO2 from tanks will be added to flue gas from coal and SRF to account for process CO2 released during calcination in a cement plant. Typical raw materials for cement production will be used as sorbent in dedicated tests.
New 1D and 3D models for hydrodynamics and heat transfer in an arrangement of heat pipes in a fluidized bed will be developed for simulations of the IHCaL reactor system. Monte Carlo Risk and Reliability Analysis will be used for risk assessment. A detailed techno-economic assessment and a life-cycle-analysis will be performed for both lime and cement applications. The basic design of a 20 MWth IHCaL demonstration plant will be developed using two different technologies, i.e. fluidized bed reactors and Direct Separation technology, and costs of these plants will be estimated.