For the application of the IHCaL process into the lime industry, Lime Plant Hönnetal (Figure 1) was used as one of the reference host facilities. The integration of IHCaL into the lime production process can be realized either as a tail-end solution in an existing lime plant (placed after the kiln and capturing the CO2 of the flue gas) or as an integrated solution, as illustrated in Figure 2. Raw material (limestone) is used as sorbent for the IHCaL process, and the purge from the IHCaL process consists of CaO, which is the main product. The heat of the flue gas leaving the carbonator or calciner could be used to pre-heat the raw material. The heat of the remaining flue gases can be extracted in heat recovery steam generators for power generation using a highly efficient steam cycle as well as for pre-heating the combustion air. The produced electricity can be partially used on site for various consumers (such as fans, pumps, mills, electrolysis for CO2 utilization) and partially sent to the grid generating additional value/income for the plant operator.
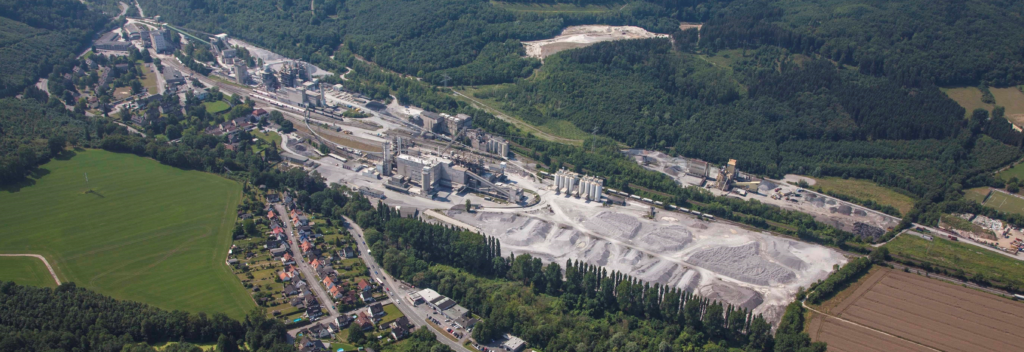
This concept results in a completely new lime production process that has various advantages compared to conventional lime kilns (such as shaft furnaces):
- The fuel is no longer in direct contact with the lime, which improves the purity of the lime and allows the utilization of “dirty” but cheap fuels, such as SRF.
- The temperature in the calciner is uniform and well controlled, which enables the production of well-designed products.
- A smaller particle size is used (0.1 – 0.5 mm) compared to shaft furnaces, which reduces the calcination time, intensifying production and minimizing inhomogeneities within the particle mixture.
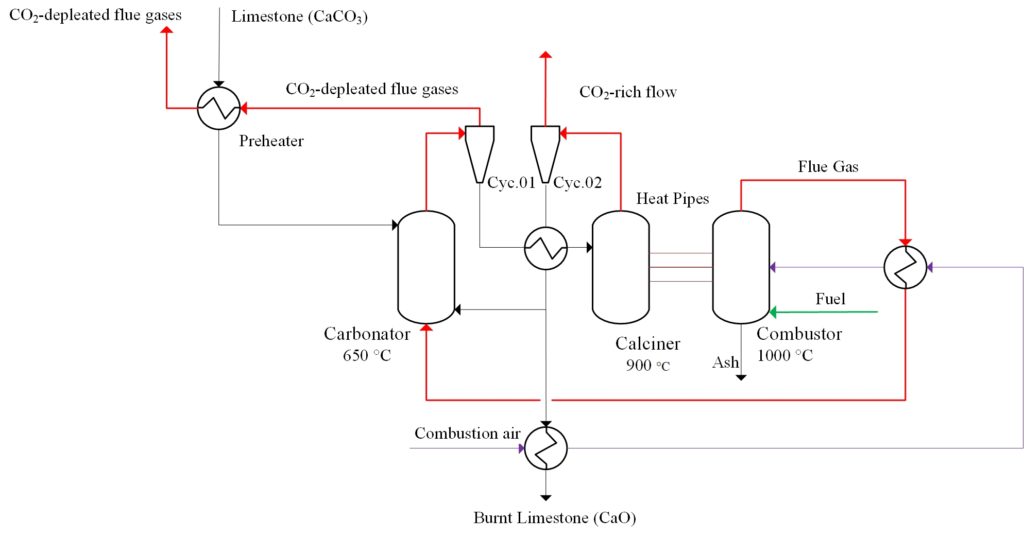