The integration of IHCaL into the cement process can be realized either as a tail-end solution or as an integrated solution using the raw meal as sorbent. A tail-end solution is placed at the back-end of the cement plant capturing CO2 from the fuel gas before being sent to the stack. This option could easily be retrofitted to existing cement plants. However, a drawback of the tail-end solution is that the process CO2 is released twice, and the solids mass flows in the IHCaL reactor exceed that of the cement plant, leading to rather huge plant sizes. Although the energy penalty is low since the additional fuel introduced into the combustor is efficiently converted to power, the economical performance is questioned due to the rather high investment and high additional fuel consumption in market of strongly varying revenues for electricity.

The integrated solution could offer significant benefits compared to the tail-end variant, as calcium carbonate is a main constituent of cement clinker raw materials, and the kiln system already includes a calciner. One possibility for such an integrated solution is illustrated in Figure 2. Raw materials for clinker production (mainly limestone) are used as sorbent for the IHCaL process, and the purge from the IHCaL process (mainly CaO and other oxides from silica, alumina, and iron) is fed to the cement kiln. Hence, the calciner of the IHCaL unit replaces the pre-calciner of a conventional cement plant. The flue gas leaving the carbonator (and/or calciner) is used to pre-heat the raw materials, potentially using existing cyclone arrangement of the cement plant. Excess heat of the calciner/combustor is extracted in heat recovery steam generators for power generation in a highly efficient steam cycle (potentially utilizing parts of an already existing power plant on the cement production site) and for pre-heating the combustion air. The produced electricity can be partially used on site for various consumers (such as fans, pumps, mills, electrolysis for CO2 utilization) and partially sent to the grid generating additional value/income for the plant operator.
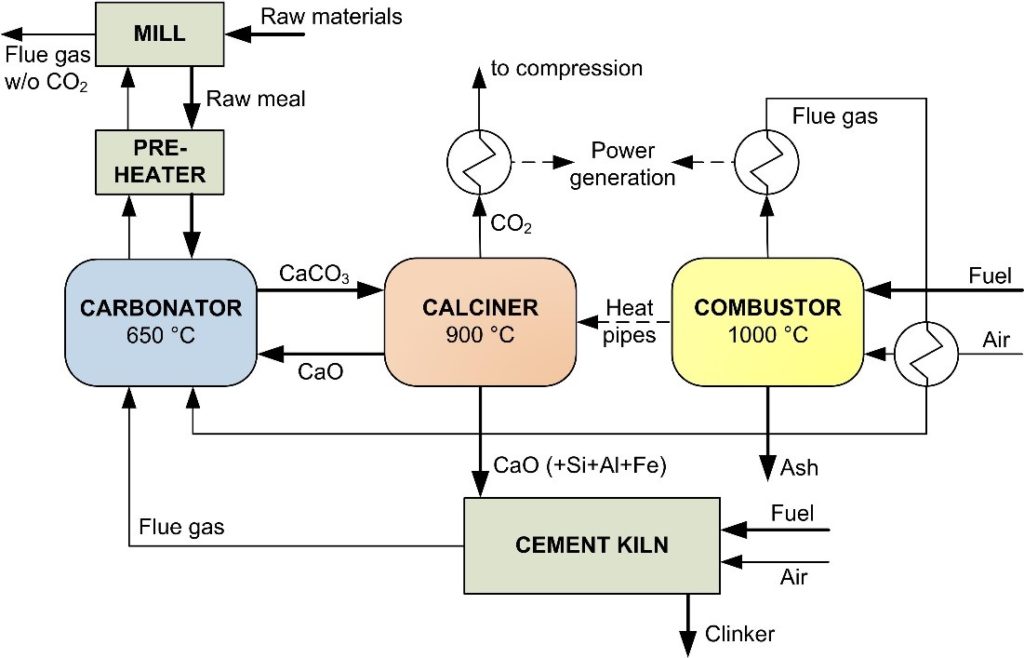